HOW AND WHY DURAFORCE™ WORKS...
DURAFORCE ™
delivers an IMPROVED REALM OF SCIENCE for these reasons:
-
Uniquely CAPTURES, RETAINS & DELIVERS GREATER ENERGY BACK to an assembled joint.
-
Not only does the Annulus clamp upon the Bolt when compressed by its matching Compression Collar, its slots allow an expansion and contraction thereof to create an INTERNAL SPRING.
-
Prevents Vibration Loosening by directly acting against the relative motion of “Side-Sliding” between Nut & Bolt threads.
-
Never before has a LATERAL FORCE been integrated into a threaded fastener system to deflect SHOCK & VIBRATION.
-
FEA MODELING ANALYSIS determines most optimum product designs.
Two different studies by North Carolina State University (NCSU) Department of Mechanical & Aerospace Engineering prove the science behind the DuraForce Fastener System.
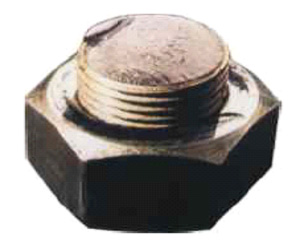
It is commonly observed that nuts and bolts when used on vibrating structure are subjected to a
phenomenon called 'vibrational loosening'. The main cause for this is the side sliding of nut or
bolt head relative to the joint. This movement causes relative motion between the threads of the
nut and bolt. The self-loosening causes a reduction in the clamp force which results in joint slip.
As a consequence of this, the bolt is subjected to bending loads and finally fails by fatigue.
Figure 1: Bolt failure caused by fatigue [1]
The main reasons of relative motion are: bending of parts that causes induction of forces at the
friction surface, differential thermal effects cause by temperature or material difference, applied
forces on the joint can lead to shifiing of the joint surfaces leading to relative motion and hence loosening.
To address this problem of self-loosening, a new mechanism is proposed where a bolt with an... |
annulus is surrounded by a collar circumferentially. When the bolt is pushed into the collar, the
annulus will deflect inward while the collar would deflect outward. This way both the annulus
and the collar will store strain energy in them. Now, when there is motion of the two surfaces
being held together by the bolt and collar which might lead to loosening, the stored strain energy
would help to keep the ioint tight. |
This FEA Modeling Illustration shows an exploded view of the
DURAFORCE™ Nut
highlighting the LATERAL FORCE created
in the compression between the Annulus and Collar
The Bolt Annulus with Compression Collar version of the product was used to simplify the FEA Modeling and better focus upon the interaction between the Annulus and Compression Cavity
The NCSU FEA Modeling Illustrations below show some parameters of the study...
Deformation comparison
A: Static Structural
Directional Deformation
Type: Directional Deformation (X Axis)
Unit: mm
Global Coordinate System
Time: 1
10/10/2012 12:05 PM
|
0.077506 Max
0.020052
0.002609
0.0051557
-0.0021976
-0.0091509
-0.017104
-0.024654
-0.032111
-0.039564 Min
|
|
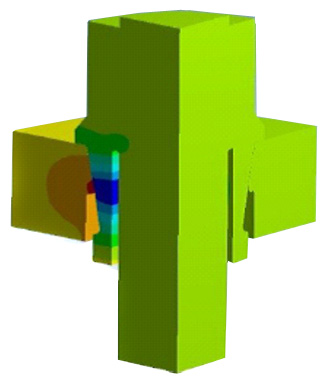 |
X axis deformation -
Maximum value = 0.0395 mm
Deformation at the collar tip = 0.0275 mm
|
A: Static Structural
Directional Deformation
Type: Directional Deformation (Z Axis)
Unit: mm
Global Coordinate System
Time: 1
10/10/2012 12:01 PM
|
0.025597 Max
0.0 10050
0.01111
0.0038057
-0.0033366
-0.01062
-0.017003
-0.025006
-0.03235
-0.039593 Min
|
|
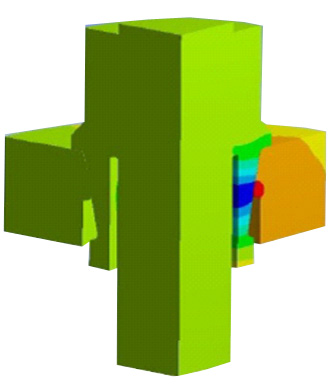 |
Z axis deformation -
Maximum value = 0.0395 mm
Deformation at the collar tip = 0.0255 mm
|
A: Static Structural
Directional Deformation
Type: Directional Deformation (X Axis)
Unit: mm
Global Coordinate System
Time: 1
5/10/2012 12:49 PM
|
0.025009 Max
0.018072
0.010835
0.0035905
-0.0036396
-0.010477
-0.018114
-0.025351
-0.032588
-0.039825 Min
|
|
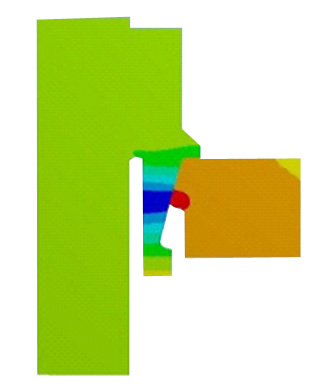 |
2D result, coarse mesh -
Maximum value = 0.0398 mm
Deformation at the collar tip = 0.0253 mm
|
A: Static Structural
Directional Deformation
Type: Directional Deformation (X Axis)
Unit: mm
Global Coordinate System
Time: 1
10/10/2012 3:05 PM
|
0.026515 Max
0.019031
0.011546
0.0040613
-0.0034234
-0.010908
-0.018393
-0.025877
-0.0022262
-0.040847 Min
|
|
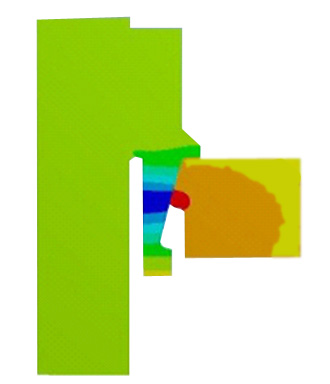 |
2D result, fine mesh -
Maximum value = 0.0408 mm
Deformation at the collar tip = 0.0265 mm
|
The NCSU FEA Modeling Graphs and Charts below document some of the
results used to design the DURAFORCE™ Fastener Systems
Figure 21: Force reaction values with over-feeding
The force reactions for the all the cases are tabulated below in table 11. It is noted that as the
angle increases, the force reaction increases and for a particular angle value, force reaction is
greater for the frictional case since greater force is required to overcome fiiction to close the
joint. It is to be noted that the values reported below are half of the actual forces that will act on
the model since one half of the model is analyzed. Therefore, to get the total force reaction, all
the values in table 11 need to be multiplied by a factor of 2.